中村宗和(本会元副会長、鳥取大学元副学長、現名誉教授、元千代田化工建設(株)常務取締役)
資源・エネルギーと触媒
原油・石炭などの化石燃料資源は、単なる蒸留や精製だけではなく、化学反応によって変化させられ、ガソリンや都市ガスなど使用しやすい形態になって、主にはエネルギー源として人々に供給されます。この過程でさまざまな触媒反応が利用されています。
環境触媒
化石燃料から得られるエネルギーの多くは火力発電所で電力に変換されます。またこれに匹敵する多量のエネルギーが自動車などの輸送機関に用いられます。これらの燃焼過程では、野放しにすれば多量の環境汚染物質が発生します。その環境負荷を抑制するために、環境触媒が用いられています。電力・自動車の両産業は、環境触媒の支えがあるからこそ、この狭い国土で高密度の発展をすることができたといえます。
そこで、このような資源・エネルギー・環境関連の触媒について解説します。触媒はプラスチック、医薬品、機能材料、油脂などの化学製品を作る過程でも使われていますが、ここで取り上げる資源・エネルギー・環境関連の触媒は、その使用量と人類社会に対する影響が非常に大きいことに特徴を持ちます。ここでは、製油所や石油関連産業の巨大なプラントで使われたり、自動車用など非常に多くの数量が使用されるこれらの触媒を紹介します。
なお、化学産業一般では均一系触媒(主には、反応物が液体で触媒も液体)も広く使用されていますが、この分野で主に使われるのは不均一系触媒(つまり、反応物が気体や液体で触媒が固体)です。固体触媒について、個人的な体験も交えて紹介します。
触媒とはどんな物質か、そこで行われる化学反応とはどんな物質変化かを順次述べると、たとえ分類しても、分厚い便覧になってしまいます。ここに述べたとおりです。しかし、資源・エネルギー・環境関連で使われる主要な触媒物質と化学反応をいくつか挙げてみると、なんとそれは暗記できるほど単純な話です。以下の話は、資源・エネルギー関連触媒と環境浄化触媒に2分しましたが、前者に分類した石油類の脱硫触媒はクリーン燃料製造という面からは環境浄化触媒にも分類できます。人によって分類に違いがあるので注意してください。
資源・エネルギー関連触媒
- 流動接触分解触媒・・・・・・SiO2・Al2O3
- 接触改質触媒・・・・・・・・Pt, Re/Al2O3
- 脱硫触媒・・・・・・・・・・MoS, NiS, CoS/Al2O3
- 水蒸気改質触媒・・・・・・・Ni/Al2O3
環境浄化触媒
触媒の種類は数多く、本一冊分も勉強しなければいけないと思いきや、実は資源・エネルギー・環境関連の触媒に限ると、上記のように特定の金属と金属酸化物、わずかな金属硫化物だけなのです。現実の触媒では、第2、第3の添加成分もあるし、担体に至っては、物理構造や酸性度といった別の要素も加わってきます。しかし、ものごとを例外から入る姿勢は応用編に譲って、ここでは、触媒成分を超単純化してみたことを重ねて強調しておきます。
なお、ここでは取り上げなかったものの、工業的触媒という視点からは、アンモニア合成触媒、エチレン・プロピレンの重合触媒も重要であることを付記します。
石油類の流動接触分解触媒
人類が地中から石油を汲み上げて、積極的に使うようになった歴史は、案外短いものです。1859年、アメリカのペンシルバニア州で、掘削技師ドレークが人類ではじめて、石油を採る目的の井戸を掘り、20bbl/d (バレル/日、20bbl = 3.2m3)の生産に成功しました。19世紀の石油は、主として灯油を得るためのもので、揮発性の高いガソリン留分や重質留分は厄介な廃棄物でした。しかし、エジソンの電灯が灯油にとって代わると、今度は、ダイムラー・ベンツによる内燃機関が発展してきました。自動車エンジン普及に伴って、石油の利用はガソリンの利用に重点を移していきました。
20世紀に入って、自動車が急激に普及し始めると、ついにガソリン不足を生じる事態となりました。ここに、石油の重い留分を分解して、より軽いガソリンを増収するプロセスが次々と開発されました。1935年ごろまでのプロセスは熱分解反応が中心で、本稿の触媒は「いまだ夜明け前」の感でした。しかし、この間に、“石油と触媒の初めての出会い“がありました。それは「触媒が分解反応速度を高める」という発見でしたが、これを、初めて商業的規模で成功させたのは、1936年のフードリー・プロセス(Foudry Process)ですから、今から僅か70年前のことです。触媒はシリカ(SiO2)・アルミナ(Al2O3)でした。
石油の分解反応は触媒上へのコーク析出との戦いで、このプロセスでは、固定床反応器を並べて、反応と再生を繰り返しました。フードリー・プロセスは触媒を利用することによって、反応速度を上げたばかりでなく、熱分解とは異なった反応機構のおかげで、価値ある新ガソリン(オクタン価の高い接触分解ガソリン)を生み出しました。その後、戦争による航空ガソリン需要の増大に向けて、触媒の利用方法を抜本的に変更した流動接触分解(FCC、 Fluid Catalytic Cracking)プロセスが誕生しました。これは、今日も石油分解法の中心的存在として、触媒・プロセスの両面から改良・発展しているものです。
流動接触分解触媒は名前の通り、流動状態で使用されますが、今日の反応器は触媒の流動というより、反応原料の流れに乗せた輸送状態であるといった方が正確です。触媒は、60ミクロン(60マイクロメートル)ほどの球形に造粒してあり、反応物質と分離された後、再生塔で触媒上に析出したコーク質を燃焼除去されます。このように流動接触分解触媒は反応器と再生塔の間を激しく循環し、再生塔では高温の水蒸気に晒されることから、大きな機械的強度と耐水熱性が要求されます。
フードリーによって初めて見出されたころの触媒は天然の活性白土でしたが、まもなく、より高活性の合成シリカ・アルミナに変わり、1960年代以降は合成Y型ゼオライトが用いられています。
20世紀は「石油の世紀」といわれたほど、自動車・飛行機・ストーブ油・石油化学原料に多量の石油が用いられました。これらは白油と俗称される石油軽質留分です。石油は連産品ですので、これらの需要が伸びれば、それに伴って重質留分も生産されます。ここに、減圧軽油(VGO)などの重質留分を軽質化する分解装置としての流動接触分解装置の重要性があります。しかも、このプロセスは、分解反応が触媒上へのコーク析出を伴う吸熱反応であることを逆手に取って、反応熱供給に析出コークの燃焼を活用するという自己完結型長所を有していました。
近年、白油需要の高まりとともに、軽質化の方法としての接触分解プロセスへの期待が高まる一方です。しかし、原料油が残油(Residual Oil)まで重くなると、原料油中に含まれるニッケル(Ni)やバナジウム(V)などの金属までも触媒上に、多量に堆積するようになりました。残油接触分解(RFCC)触媒では、このような耐メタル性など、増える一方の要求事項を満たすための触媒改良が続けられています。
石油類の接触改質触媒
石油を蒸留して得られるナフサ留分はそのままではオクタン価が低く、今日の高圧縮比のエンジンには向きません。圧縮比を大きくできれば、それだけ輸送性能も向上しますが、その分オクタン価の高いガソリンが必要となります。オクタン価の高い成分とは、芳香族、オレフィン、イソパラフィンで、逆に低い成分は直鎖パラフィンです。ナフテン類のオクタン価はその中間に位置します。直留ナフサに含まれるナフテン類を脱水素して芳香族にするとともに、直鎖パラフィンを環化脱水素して芳香族や水素化分解してイソパラフィンに変換する画期的プロセスが1949年に開発されました。直留ナフサから、芳香族成分に富んだガソリンを製造する操作を接触改質(リフォーミング)といい、ここで用いられる白金(Pt)–塩素添加アルミナ触媒は、代表的二元機能触媒とされます。
接触改質プロセスが爆発的に増えた背景には、当時のアメリカのモータリゼーションや高速道路時代がありましたが、このプロセスは、他にも優れた点を持っています。それは、このプロセスが石油化学原料としてのベンゼン・トルエン・キシレン(BTX)製造プロセスにもなることと、脱水素反応に伴って得られる多量の水素を、安価に併産できる点です。
開発以来20年間ほどは、触媒成分のPtにちなんで、このプロセスはプラットフォーミングと呼ばれました。しかし1960年代後半になって、にわかに改良触媒が出始めました。それがPtにレニウム(Re)を添加したバイメタル触媒で、錫(Sn)やイリジウム(Ir)などを加えたマルチメタリック触媒でした。
脱水素反応は、熱力学的には低圧が有利であるにもかかわらず、接触改質プロセスは500psig (psig: ポンド/平方インチ、500psig = 3.5MPa、およそ35気圧)程の水素加圧下で運転されてきました。これは、触媒劣化要因であるコーク析出を少しでも抑制しようとするものでしたが、これらの新しい触媒は、コーク析出が少なく、より低圧運転を可能とするものでした。さらに、1970年代に入ると、この新しい触媒の特性を生かした新しいプロセスが誕生しました。それは、触媒を反応塔から再生塔へゆっくり循環移動させるもので、新触媒の耐コーク性を利用しながらも、運転中の触媒再生をも実現したことによって、改質反応としては、究極の低圧運転を可能にしたものでした。プラットフォーミング触媒の特許は、一世を風靡した画期的なものとして有名ですが、その後の改良触媒が、プロセス改良を呼び、プロセス改良がさらなる触媒改良を呼ぶという好循環の典型例となったものです。
石油類の脱硫触媒
各種の石油製品は、沸点の低い成分から、高い成分まで多成分を含む原油を蒸留することによって得られます。得られた各留分は、多かれ少なかれ有機硫黄化合物を含みますので、これを燃焼するときに発生する硫黄酸化物(SOx)を事前に除去する目的で、石油類は脱硫されます。xには種々の値がありますが、大部分は二酸化硫黄(SO2)です。ガソリンとなるナフサ留分、ストーブオイルとなる灯油、ジェット燃料、ディーゼル燃料、発電などのボイラー向け重油などは、それぞれに対応した反応条件で、水素化脱硫されます。この際使われる触媒も、対象とする留分ごとに最適化されたものが使われますが、多くはアルミナ(Al2O3)担体に主にモリブデン(Mo)を、補助的にニッケル(Ni)、コバルト(Co)を担持したものです。通常、触媒工場から出荷されるとき、担持金属は酸化物状態ですが、使用前に硫化され、硫化金属として反応機作に関与しています。時として、製油所における硫化作業を合理化するため、硫化触媒として出荷されることもあります。
原油に含まれるもっとも重い留分である「残油」は、大きな分子を含み、硫黄化合物も難反応性です。したがって、残油の脱硫条件は過酷なものとなり、触媒使用量も大きなものとなります。一例を示すと、一機の反応器に充填される触媒容積は300m3にもなり、これを充填する作業も壮観なものとなります。通常、触媒は200リットル(0.2m3)のドラムに充填して出荷されますので、ドラム数は1500本となります。これを高さ30mの反応器の入り口マンホールまで連続的に運び、定められた充填法で、反応器下部から上に満たして行くことになります。反応器内部にいる作業者は、その特殊環境から、エアラインマスクをつけての作業となりますが、厚さ30cmの反応器壁で外界から遮断された世界は、異様な気分にさせるものです。このように大きな反応器の場合、上から流れ落ちる反応原料油が均一になるよう、内部構造上の工夫をする他に、触媒にも、形状・充填密度・機械的強度などの点で、厳しい仕様が要求されます。
石油の各留分は、元来含まれる硫黄分濃度が違う上、脱硫されやすさも各留分で異なります。現在のガソリンや灯油は、ほとんどサルファーフリーまで脱硫されていますが、軽油には50ppm(重量百万分率)ほどの硫黄分が含まれています。しかし、30年前までの日本の軽油は、12000ppmもの硫黄を含んでいたことと比較すると、1/240にも低減されたことに驚くばかりです。
硫黄酸化物は石油燃焼以外に、主に石炭燃焼火力発電所でも発生します。こちらは、排煙脱硫装置によって除去され、結果として日本は世界一清浄な大気のもとで生活できています。
わが国は、国土面積あたり産業集積度が高い(エネルギー消費量が大きい)ため、過去の高度成長期には、大気の汚染が進みました。脱硫触媒と脱硫プロセスの進歩、普及によって、わが国の空が、いかにきれいになったかは、環境白書が鮮明に物語っています。
炭化水素の水蒸気改質触媒
水素は石油類の水素化脱硫に際して、また種々の水素添加反応の還元剤として大量に用いられます。また、アンモニアやメタノール製造の原料でもあります。水素の製造については、石油類の接触改質触媒の項で、接触改質反応に伴って副生する水素について述べましたが、増大する一方の水素需要をまかなうために、炭化水素の水蒸気改質反応が利用されるようになりました。一般に水素を製造するというと、水の電気分解による水素を思い浮かべる人が多いと思いますが、その利用はきわめて限定された分野です。わが国では、燃料油の使用量増大と、水素化脱硫の脱硫度強化が、水蒸気改質プロセスを急激に増大させました。他方、発展途上国では、食料増産のためのアンモニア需要がこのプロ)セスの普及の原動力でした。
水蒸気改質触媒はアルミナなどの担体にNiを含浸させたものが使われます。この触媒は微量の硫黄にも被毒されるので、原料となる天然ガス、液化石油ガス、軽質ナフサなどは、水蒸気改質に先立って徹底的に脱硫されます。水蒸気改質触媒は、他のプロセス触媒とは異なった形状をしています。多くは、蓮根を輪切りしたような形を採用しています。それは、この反応が極めて速いことに対応するとともに、高い圧壊強度、低い圧力損失を実現するための工夫です。
水蒸気改質反応は大きな吸熱反応なので、多数の管型反応器を加熱炉の中に配置するなど、反応熱を効率よくプロセス流体に与えるための種々の工夫がなされています。生成物は水素を主としますが、他に一酸化炭素(CO)と少量の二酸化炭素(CO2)も含みます。前者は水性ガスシフト反応によってさらに水素に転換し、二酸化炭素は分離されることによって、水素が単離されます。
水蒸気改質反応の平衡定数は非常に大きく、原料炭化水素中の水素はもちろん、ガス化剤である水蒸気の水素も水素源となっています。したがって炭素析出のない場合の生成物組成はシフト反応とメタン化反応の平衡を考慮すれば算出できます。現実には、装置と運転コストの経済性も考慮されて、水蒸気/炭素比(H2O/C): 約3、反応温度: 約800℃、反応圧力: 約20気圧(2MPa)で運転されます。
水蒸気改質反応では、触媒上への炭素析出がしばしば問題視されます。これは、生成物である一酸化炭素や少量のメタン(CH4)が不均化反応によって炭素を析出させるもので、触媒活性の低下はもちろん、時に触媒を内部から崩壊させたり、反応管の閉塞などのおおきなトラブルを起こします。現実には、これらの反応平衡を考慮して、反応温度、反応圧力に対応する炭素析出を起こさない最小の水蒸気/炭素比(H2O/C)以上の領域で運転することとしています。
排煙脱硝触媒
燃焼に伴って大気中に放出される窒素酸化物は主として一酸化窒素(NO)で、少量の二酸化窒素(NO2)を含みます。両者を併せてNOxと呼びます。SOxの生成は、かならず燃料中の硫黄化合物に起因する(ここ参照)のに対して、NOxには、燃料中の窒素化合物が燃焼という酸化反応で転化するもの(これをFuel NOxという)と燃焼空気中の窒素と酸素が高温状態で反応して生成するもの(これをThermal NOxという)があります。したがって、前述した石油類の脱硫のように、燃料を事前に脱窒素したとしても、燃焼排気ガスは必ず、窒素酸化物を含むことになります。Fuel NOxは燃焼域での酸素濃度が高いほど多く発生します。Thermal NOxは燃焼域での酸素濃度が高いほど、燃焼温度が高いほど、滞留時間が長いほど多量に発生します。
工業用の燃焼装置からでるNOxを減らす原理は、上述の生成原因を潰せばよいことですが、燃料中の窒素分を除去することは、脱硫以上に困難です。Thermal NOxを減らすための、酸素濃度低減・燃焼温度低下・滞留時間短縮も、実施されているものの脱硝には限度があります。
結局、火力発電所や工場の大型ボイラーの排ガスには、発生したNOxを、排ガスから除去するアンモニア選択接触還元法(SCR法)が用いられます。この方法は、数%の燃焼残酸素と数百ppmのNOxを含む排ガスに、NOxと当量程度のアンモニアを添加して、触媒上で窒素と水への還元反応を行わせるものです。
100万KWの火力発電所が出す排煙は1時間に330万m3(東京ドーム4杯分)にも及び、排煙脱硝触媒は、大量の排ガスを少ない圧力損失で処理することが求められます。したがって、この触媒はハニカムまたはプレート状に加工したチタン(Ti)・バナジウム(V)系が一般的です。
自動車触媒
排ガス規制は、当初大型の固定発生源である諸工場から始まりましたが、それらの排ガス処理が進むにつれて、自動車などの移動発生源からの環境汚染が重要視されるようになりました。もちろん、自動車台数の増加という、排ガス量の増大という背景もあって、自動車排ガスの規制は年々強化される方向です。
自動車にはガソリンを燃料とするガソリンエンジンと軽油を燃料とするディーゼルエンジンがあり、一般に、ガソリン車は乗用小型車に、ディーゼル車はバス・トラックなどの大型車に使われます(注: ヨーロッパでは、乗用ディーゼル車も多い。両者の排ガス特性は、燃料と燃焼方式の違いを反映して、大いに異なります。
ガソリン車の排ガスに含まれる環境汚染物質は主に、NOx、炭化水素(HC)、COです。1970年代後半、これらを同時に除去する三元触媒が開発されました。これは、一体型成形(モノリス)されたハニカム状コージライト(2MgO・2Al2O3・5SiO2)担体に多孔質アルミナを塗布し、これに白金(Pt)、パラジウム(Pd)、ロジウム(Rh)などの貴金属を含浸担持したものです。
三元触媒の働きは、ここに示すように、性質の異なる反応を同一触媒上で実現した点で画期的ブレークスルーでした。NOxの還元には、当然還元領域(酸素の少ない領域)が好都合ですが、酸化反応であるHC、COの燃焼にとっては、不都合で除去率が低くなります。HC、COの酸化にとって好都合の酸素の多い領域では、NOxの除去がうまくできません。このようなしがらみの中で、理論空燃比14.6の前後(僅かに開いた窓: ウインドウと呼ばれる)では、NOx、HC、COすべてが、約90%の除去率で浄化されます。
自動車のマフラー触媒は化学プラントの反応器に充填されて利用される触媒と異なり、反応ガスの濃度や温度などの反応条件が、エンジンの駆動状態とともに変化する過酷な条件に耐えなければなりません。加えて、振動や長期間使用に耐える耐久性も要求されます。担体にコージライトというセラミック結晶を用いるのは、この材料の熱膨張係数が小さく、耐熱衝撃に強いからです。しかし、このままでは、貴金属の分散がよくないので、結晶表面をアルミナ層で覆ってあります。
この触媒開発の成功なくして、自動車の普及を語れないほど、貴重な存在の触媒です。しかし、触媒は自動車の排気パイプのエンジンとマフラーの間という、人の目にふれない車体の裏側に取り付けてあります。まさに縁の下の力持ちとは、この触媒を指すと言ってよいほどです。
もう一方のディーゼルエンジンの排ガスには、燃料中の硫黄分にもとづく硫酸塩や不完全燃焼に由来するタール状のもの(粒子状物質: パティキュレートあるいはパティキュレートマターPMと呼ばれる)とNOxが含まれます。これらは、ガソリンエンジンに適用された三元触媒では処理できず、従来、エンジン内の燃焼を改善する方法で抑制が行われてきました。排ガス再循環などの燃焼温度を下げる方法はNOxの低減に有効ですが、逆に粒子状物質を増加させる傾向にありますので、後処理装置の開発が急がれているところです。
私にとっての触媒との出会い
触媒という言葉の意味は、なんとなくわかって、完全にはわからないものです。私が初めて触媒に出会ったときも、触媒とは『化学反応を起こすとき、反応物質以外のもので、それ自身は化学変化を受けず、しかも反応速度を変える役目をする物質』と教わり、自分では、理解できたつもりでいました。しかし、この教科書的な解説では、教えてくれた先生も、生徒に理解させたという自信が持てないようです。したがって、触媒の解説本では、多くの化学反応が例示されることになります。ここで、“多くの化学反応が例示される“と、断ったのは、化学反応の種類によって使われる触媒が違うからです。これがまた触媒の理解を邪魔している理由でしょう。「触媒とは」にも、代表的触媒物質、触媒反応の機作について上手な説明がなされています。各種の便覧を紐解くと、反応の種類と、対応する触媒が数百ページにわたって掲載されています。
今日、触媒作用が認められている物質には、気体状のもの、液状のものもあり、もちろん固体触媒は商業触媒の中心的存在です。触媒反応自身は、われわれが科学的知識を獲得する以前から、自然界の反応でも起こっていましたし、なによりわれわれの体内の複雑な酵素反応も触媒反応です。まして、産業界で利用される化学反応は、反応速度を上げる(反応器サイズを下げる)目的で、その大部分は触媒反応と言ってもいいほどです。こうなると、私の若いときの苦い思い出“あれも触媒、これも触媒。あれも触媒反応、これも触媒反応。それぞれはみなその中身が違うでは、もう嫌になっちゃう!”が偽らざる気持ちでしょう。
ここでは、不正確になりますが、詳細部分は敢えて切り捨て、産業社会的に重要な触媒を摘み出してみることとします。すると、それはある種の形に成型された(反応効率を上げたり、取り扱い易くする)固体触媒であることが多くの場合です。大きさや形は、さらさらと流れる粉状のもの、丸薬のような丸いもの、折れた鉛筆の芯のような円筒形のものなどいろいろあります。
写真提供: 日本ケッチェン株式会社
注: 写真の著作権は日本ケッチェン株式会社にあります
The following photographs were kindly supplied by Nippon Ketjen Co.,Ltd.
(C) Nippon Ketjen Co.,Ltd. All rights reserved
これらの内部には、反応分子が入っていく無数の細孔が開いているといいます。しかし、その細孔は小さくて見えません。見えないほど小さな孔が無数にあいているので、その細孔で構成される表面積は非常に大きなものとなります。通常、細孔直径は小さいもので1nm、大きなもので100nmぐらいです。この孔に入って行って、反応する分子の大きさが、これより小さいので、これくらいの大きさが選ばれるのです。
私が初めて触媒に出会ったとき、この細孔で構成される触媒の表面積Sは、(1)式で表されると習いました。当然ながら、細孔直径Dが小さくなるほど、Sは大きくなります。
(1)式
S: 比表面積
V: 細孔容積
D: 細孔直径
(1)式より、Vが0.4cm3 / g = 4×10-7m3、Dが10nm = 10-8mの脱硫触媒1gが持つ表面積は160m2にも及ぶと計算されます。脱硫触媒1gがもつ表面積は、高級住宅地の敷地面積ほどにもなります。まして、活性炭触媒やゼオライト触媒のように、Dが1nmと小さくなると、1gあたり1600m2にもなります。事実、窒素吸着法で測定した表面積もほぼこの数値を示しますが、私には、実感を伴いません。
それは、この式が誘導される模型図によって、悪い頭が、さらに混乱させられたことにもよります。上記の触媒表面積、細孔直径、細孔容積の関係は図1の触媒細孔モデルを使って説明されました。
この円筒状の細孔が持つ
表面積(2)と
円筒体積に相当する細孔容積(3)
の両式からLを消去すると、先ほどの(1)式が得られます。この式は、石油の重い留分(分子が大きい)を反応させる触媒を設計する際には、特に重要な関係式となります。
この細孔モデルによって、触媒の内部構造について、私が勝手に描いたイメージは、ちょうど地中に作られた蟻の巣のようなものでした(図2)。
触媒物質の中に細く長いトンネル状の孔を、しかも行き止まりのトンネルを想像した私は、「触媒というのは、どうしてこんなにうまく、反応を進行させるのか」と半分疑問に思い、しっくりしないまま卒業してしまいました。私が勝手に頭に描いた想像図ですから、誰も修正してくれないまま、後年、会社で触媒を設計する立場となりました。
後述するように、会社に入って20年後に、この触媒内部構造のイメージが白黒反転するほど変わりました。それは、科学技術の進歩で、目に見えなかった細孔が見えるようになったからです。
イノベーション現場の触媒
入社して初めて理解した触媒の本質
入社後、私に与えられ仕事はプロセス開発でした。新しいプロセスは、プロセス条件を一新するもの、反応原料や生成物を一新するものなど広範囲ですが、新プロセスといえるものの多くは、触媒の出来不出来に依存していることに気づきました。回りを見れば、メーカーはもちろん、エンジニアリング会社、ユーザーまで、多くの人が新触媒の開発を競っていることを知りました。
化学原料を供給する会社、医薬品・化学製品を作る会社はもちろん、石油・ガスのようなエネルギー供給会社、鉄・セメント・紙パルプなどの資源を加工する会社まで、触媒を使う反応は多く用いられています。また、発電は電力へのエネルギー転換に際して、自動車はガソリンや軽油を燃焼する過程で、大きな環境負荷を与えます。両産業は、環境触媒の支えがあるからこそ、この狭い国土で高密度の発展をすることができたといえます。
新製品の開発をしている人、新プロセスの研究をしている人がさまざまな分野で、日夜奮闘しているのを目の当たりにした私は、触媒の種類や化学反応が違えども、これらの人の多くが触媒の研究をしているということにおどろきました。そして、触媒というものが、こんなにも重要な働きをしており、産業界にとって「鍵」や「扇の要」といわれるのに、案外、高校教育も大学教育も触媒に割く時間が少ないなーと恨んだりしたものです。
その後、会社に入って10年ほどたったとき、触媒のことをWiseman’s Stone(賢者の石)とも言うと聞きました。確かに、その役割は、西洋中世の錬金術師が、卑金属を金に変化させる夢を探し求めた話に似ています。近年、日本の国際的地位がキャッチアップ型からフロントランナーに変わってきました。それに伴って、日本は科学技術立国・知的財産立国を国是として、21世紀を生きようとしています。そのとき、多くの人がWiseman’s Stoneに注目するのは、触媒というものが、独創的であり、知的財産的であり、省資源的な科学技術として期待を集めるからです。
会社に入って20年ほど経ったころ、私は石油残渣油のアップグレーディング(Upgrading)に取り組んでいました。反応分子がアスファルテンなど巨大なサイズになると、分子の細孔内拡散が重要になります。いきおい、触媒設計者にとっては、細孔構造の制御が触媒性能を支配する重要因子になります。先述の触媒細孔モデルで、細孔直径Dが10~20nmにもなる触媒です。
細孔径の大きな触媒を作るには、それを作る基本粒子を大きくしなければなりません。通常のこの種の触媒はアルミナ(Al2O3)担体にモリブデン(Mo)を浸漬させてつくります。自分の作った触媒の孔の中を、この目で見たかのように語れたら、どんなにか迫力のある議論ができるだろう・・と考えていたとき、このセラミックの触媒担体をダイヤモンド・カッターで厚さ50nmの超薄片にできると言う話を聞きました。一方で、年々進歩していた透過型の電子顕微鏡技術と組み合わせて、自分の調製した触媒の細孔構造を直接見ることができました。細孔径50nmのトンネル径は2万倍になると、100万nm = 106×10-9 m = 10-3 m = 1mmです。
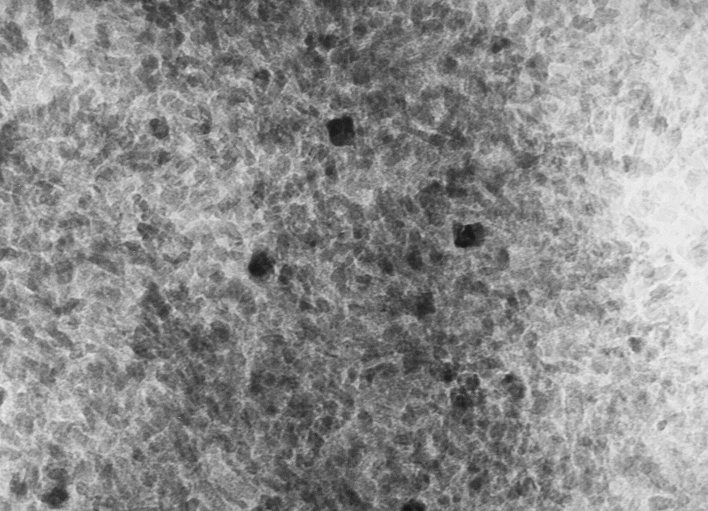
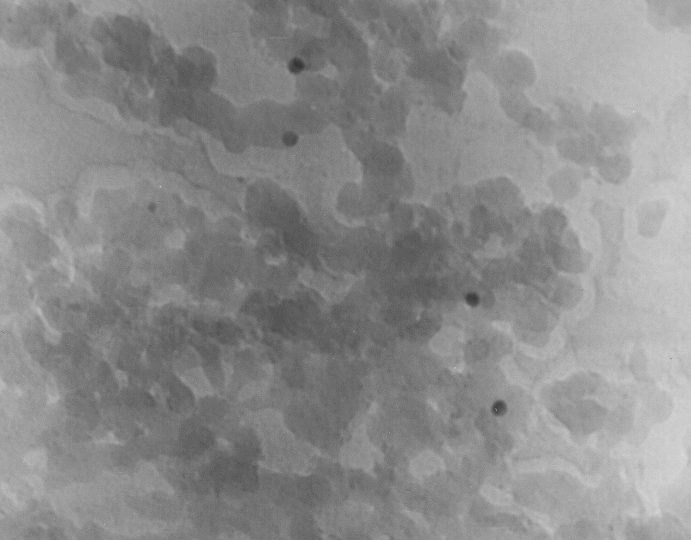
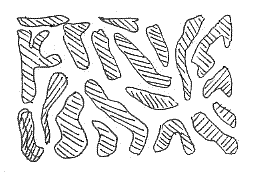
図3: Pdをわずかに含むアルミナ触媒のTEM(透過型電子顕微鏡)画像。測定された画像は200,000倍、web上では環境によってサイズが異なるが、図の横幅がだいたい300nmである。
注1: 正確に言うと、私が当時見た画像は20,000倍のアルミナのTEM像でした。この解説記事を触媒学会webページに収録するにあたり、同じ画像を使うことができなかったので、最近測定されたPdを含有するアルミナの200,000倍のTEM像を示しました。
図3は私が40歳になって見たアルミナ担体の電子顕微鏡像のイメージです。固体触媒の細孔構造として、私が学生時代に想像したトンネル構造(図2)と比べると、両者は似て非なるものです。私がアルミナ(担体物質)と思っていたトンネルの壁部分(図2のハンチング部分)は実は細孔(図3の白い部分)であり、細孔(トンネル空間)と思っていた部分(図2の白い部分)が実はアルミナ担体物質(図3のハンチング部分)でした。ちょうど、白黒逆転のフィルムを見るように、私の想像していたものと正反対でした。実は、よく考えると、基本微粒子(図3の1個の黒い部分)が集まって粉を形成し、その粉が成型されて担体となるわけですから、図3が当然であり、自分の陥った誤りが腹立たしく思われます。しかし、図3を見たときは、目から鱗が落ちる思いがするとともに、図2を脳裏に抱かせる伏線となった図1を恨めしく思ったものです。ともかく、触媒の細孔というのはトンネルではなく、柱と柱の隙間であることが分かった。同時に、こんなにも小さい世界に反応分子が自由に動き回るイメージが理解できるようになりました。この空間に浮いたような柱の太さを大きくすれば、細孔も大きくなるし、柱の太さ・長さをできるだけ揃えることが、均質な細孔を作ることになることも、容易に想像できるようになりました。